Learn about Yankee Hill Brick's History.
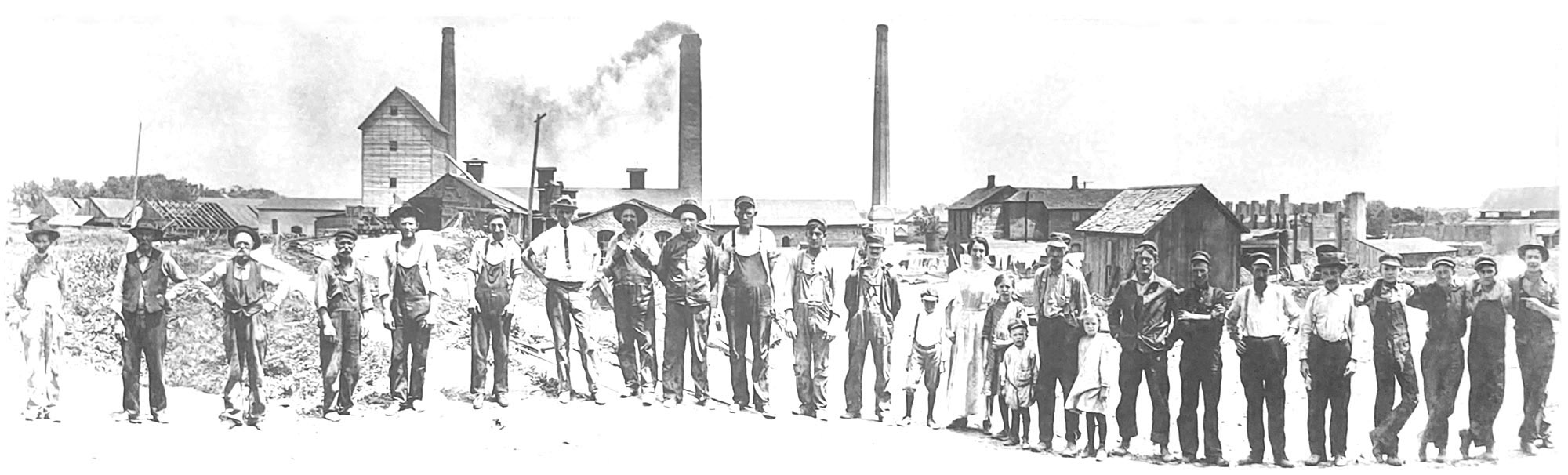
FOR MORE THAN 140 YEARS, YANKEE HILL BRICK MANUFACTURING COMPANY HAS LED THE WAY IN CLAY BRICK MANUFACTURING AND INNOVATION. FROM FACE BRICK, PAVERS AND TO SPECIAL SHAPES. YANKEE HILL BRICK CONTINUES ITS HISTORIC TRADITION OF PAVING NEW ROADS IN THE BRICK INDUSTRY.
Clay Brick History
Brick is a timeless, classic building material. The Babylonians, Chinese, and Egyptians understood the value of the simple rectangular solids more than 3,000 years ago. Invented in antiquity, brick remains the one exterior building material with a human scale, rich variegated colors, and flexibility of use. Modern man has crafted building materials from concrete, plastic, glass and steel, but none approach this unique elementary product.
The brick making process is essentially unchanged from primitive times. Clay is mixed with water to form a pliable mass. The clay is then formed with a mold, dried and baked to nearly 2000 degrees.
Brick makers brought this ancient skill from Europe with them as they landed in the New World. It was such a wide spread craft that many early Americans built their homes with bricks molded from the clay excavated from the foundations.
As Americans moved west in the 1850’s and 60’s, some passed southwest of present day Lincoln, NE. A small community of New Englanders settled in the hilly area, built a store and blacksmith shop, and named the community Yankee Hill. In 1881 Joseph E. Stockwell began to make brick from the wonderful clay deposits located a mile or so west of the village. The manufacture of brick at this same location has continued to this day.
Yankee Hill Brick was incorporated in 1902 as the Yankee Hill Brick Manufacturing Company with principle stockholders – Sumner Burnham and W.H. Ferguson. Over the years the plant has had several kilns. Early on, the brick were fired in scove kilns [rectangular masses of brick stacked loosely together, covered with clay], and fired for weeks. Later the European Hoffman kiln came into use. It used coal as a fuel and fired brick in less than two weeks. Beehive kilns with their distinctive round shape were also frequently used. Another early coal-burning kiln called a Udahli is now depicted on Yankee Hill’s logo with its multiple chambers and small smoke stacks.
The brick making process
We no longer make brick at the pace of the Egyptians. While the process is essentially the same, the advent of earth moving equipment, powerful electric motors, and modern tunnel kilns has made brick making much more automated and productive. But, we still begin with clay dug from the earth.
Clay mining and preparation
A few miles from Yankee Hill Brick we mine clay using large backhoes, dozers, and diesel trucks. We segregate the clay, which is from the 100million-year-old Dakota formation, into several colors. From the same pits weal so recover sand, essential to the process. We stockpile the clay in separate piles at the plant site and then blend them back together in specific proportions to achieve the colors for which we are so famous.
We grind the clay and sand together in a two-hundred horsepower, high-speed hammer mill, where hardened steel hammers rotating at 1150 rpm shatter the clay into small pieces. The milled mixture is screened to the consistency of coarse sand and stored until we’re ready to make it into brick.
Forming
Forming is the one manufacturing step that differs markedly from ancient times. We mix the clay with water and knead it into a pliable mass. Three-thousand years ago it was hand-made one brick at a time; now mixing is in a pug mill – a one-hundred horsepower tub with shaft-mounted knives that slice and cut the moist clay until it is uniform. Immediately after pugging we remove trapped air in a vacuum chamber, extrude the clay with a powerful auger extruder, and form it into a continuous column. The next step is a cutter, strung with piano wire, which slices the clay column into separate bricks. Once formed, we set the bricks on drier cars to ensure they are dry prior to firing.
Drying and Firing
Over a period of several days the brick gradually warm until they are bone dry. Any residual moisture would make them explode in the kiln. We then load them onto refractory lined kiln cars with steel undercarriages and narrow gauge railroad wheels. The cars enter the kiln at the cool end. Back to back in a continuous train of cars, they push one another through the tunnel kiln. They are propelled by a powerful hydraulic ram that inches them slowly down the length of the 268-foot kiln.
As one car comes out the kiln exit, another goes in the entrance. On their passage through the kiln, they gradually increase in temperature as they pass dozens of flaming, gas burners. When they reach 2100 degrees the brick are mature, having developed their color and vitrified hardness -- which makes them durable for centuries. They gradually cool until they exit the kiln thirty-six hours after they entered.
Packaging and Delivery
After cooling, we inspect the brick and stack them into neat bundles held together by strong plastic straps. The straps hold the brick together for ease of transport around the brickyard by forklifts. We then load the brick onto trucks or into railroad cars for delivery anywhere in the United States.
Clay Brick History
Brick is a timeless, classic building material. The Babylonians, Chinese, and Egyptians understood the value of the simple rectangular solids more than 3,000 years ago. Invented in antiquity, brick remains the one exterior building material with a human scale, rich variegated colors, and flexibility of use. Modern man has crafted building materials from concrete, plastic, glass and steel, but none approach this unique elementary product.
The brick making process is essentially unchanged from primitive times. Clay is mixed with water to form a pliable mass. The clay is then formed with a mold, dried and baked to nearly 2000 degrees.
Brick makers brought this ancient skill from Europe with them as they landed in the New World. It was such a wide spread craft that many early Americans built their homes with bricks molded from the clay excavated from the foundations.
As Americans moved west in the 1850’s and 60’s, some passed southwest of present day Lincoln, NE. A small community of New Englanders settled in the hilly area, built a store and blacksmith shop, and named the community Yankee Hill. In 1881 Joseph E. Stockwell began to make brick from the wonderful clay deposits located a mile or so west of the village. The manufacture of brick at this same location has continued to this day.
Yankee Hill Brick was incorporated in 1902 as the Yankee Hill Brick Manufacturing Company with principle stockholders – Sumner Burnham and W.H. Ferguson. Over the years the plant has had several kilns. Early on, the brick were fired in scove kilns [rectangular masses of brick stacked loosely together, covered with clay], and fired for weeks. Later the European Hoffman kiln came into use. It used coal as a fuel and fired brick in less than two weeks. Beehive kilns with their distinctive round shape were also frequently used. Another early coal-burning kiln called a Udahli is now depicted on Yankee Hill’s logo with its multiple chambers and small smoke stacks.
The brick making process
We no longer make brick at the pace of the Egyptians. While the process is essentially the same, the advent of earth moving equipment, powerful electric motors, and modern tunnel kilns has made brick making much more automated and productive. But, we still begin with clay dug from the earth.
Clay mining and preparation
A few miles from Yankee Hill Brick we mine clay using large backhoes, dozers, and diesel trucks. We segregate the clay, which is from the 100million-year-old Dakota formation, into several colors. From the same pits weal so recover sand, essential to the process. We stockpile the clay in separate piles at the plant site and then blend them back together in specific proportions to achieve the colors for which we are so famous.
We grind the clay and sand together in a two-hundred horsepower, high-speed hammer mill, where hardened steel hammers rotating at 1150 rpm shatter the clay into small pieces. The milled mixture is screened to the consistency of coarse sand and stored until we’re ready to make it into brick.
Forming
Forming is the one manufacturing step that differs markedly from ancient times. We mix the clay with water and knead it into a pliable mass. Three-thousand years ago it was hand-made one brick at a time; now mixing is in a pug mill – a one-hundred horsepower tub with shaft-mounted knives that slice and cut the moist clay until it is uniform. Immediately after pugging we remove trapped air in a vacuum chamber, extrude the clay with a powerful auger extruder, and form it into a continuous column. The next step is a cutter, strung with piano wire, which slices the clay column into separate bricks. Once formed, we set the bricks on drier cars to ensure they are dry prior to firing.
Drying and Firing
Over a period of several days the brick gradually warm until they are bone dry. Any residual moisture would make them explode in the kiln. We then load them onto refractory lined kiln cars with steel undercarriages and narrow gauge railroad wheels. The cars enter the kiln at the cool end. Back to back in a continuous train of cars, they push one another through the tunnel kiln. They are propelled by a powerful hydraulic ram that inches them slowly down the length of the 268-foot kiln.
As one car comes out the kiln exit, another goes in the entrance. On their passage through the kiln, they gradually increase in temperature as they pass dozens of flaming, gas burners. When they reach 2100 degrees the brick are mature, having developed their color and vitrified hardness -- which makes them durable for centuries. They gradually cool until they exit the kiln thirty-six hours after they entered.
Packaging and Delivery
After cooling, we inspect the brick and stack them into neat bundles held together by strong plastic straps. The straps hold the brick together for ease of transport around the brickyard by forklifts. We then load the brick onto trucks or into railroad cars for delivery anywhere in the United States.